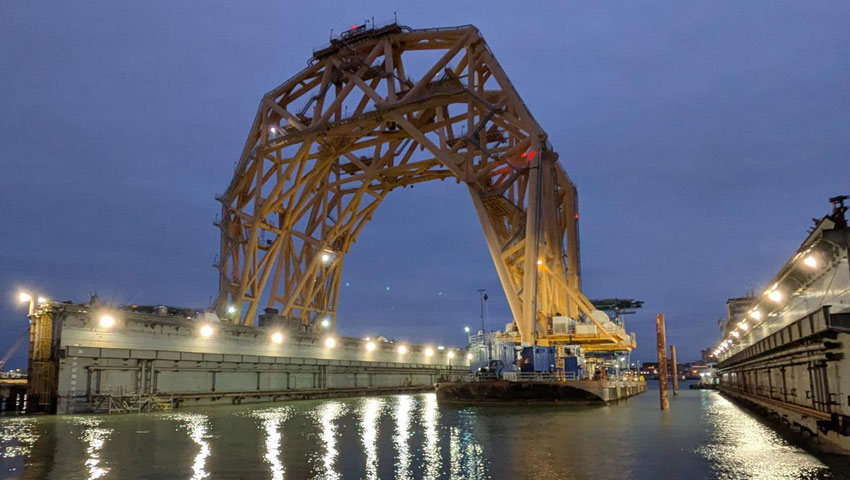
Story of the Month: The XT-10000 Project
Innovating Maritime Solutions: The XT-10000 Project
We at Gulf Copper and Manufacturing and Gulf Copper Energy Services (GCES) are excited to share some thrilling news regarding our ongoing support for the XT-10000, the largest heavy-lift vessel in the United States. Our team has been diligently working to ensure that this remarkable vessel operates at peak performance, and we are proud to announce that we will be undertaking essential maintenance during its upcoming stay at our facility on the 35,000-t dry dock in Galveston.
This maintenance will include critical tasks such as repainting and thruster servicing, which are vital for the XT-10000’s operational efficiency. Our dedicated GCES team has provided rigging, lifting, inspections, and HSE support for several years, ensuring that the vessel remains in top condition while out in the field. Our shipyard team will now dry dock the vessel.
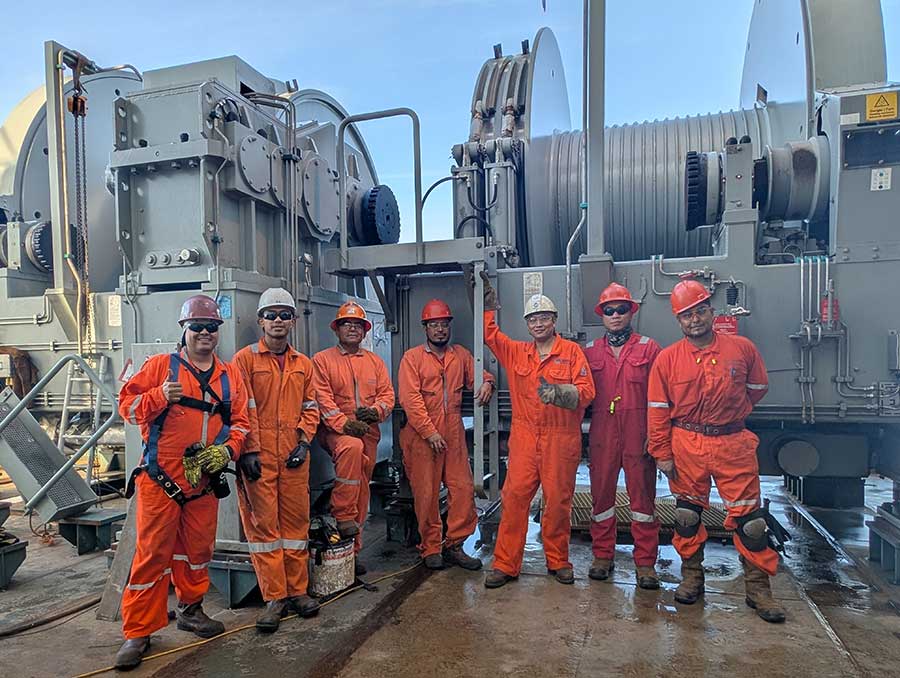
Story of the Month: Independencia II Mooring
Reinforcing Independence:
OOS-Enabled Independencia II Mooring System Upgrade
The maritime industry demands constant innovation, pushing the boundaries of logistics to achieve ambitious goals. We thrive on these challenges at Gulf Copper Energy Services (GCES). Our recent work on the OOS-enabled Independencia II, a heavy-lift vessel operating in demanding offshore environments, exemplifies our commitment to delivering complex projects with precision and efficiency. This wasn’t just maintenance but a transformation, bolstering the vessel’s capabilities and extending its operational lifespan.
The project centered around a significant upgrade to the vessel’s mooring system foundation. This involved enhancing the vessel’s structural integrity to accommodate two fairleads on each column and two winches on each deck’s four corners—a crucial upgrade for increased stability and operational flexibility in challenging offshore conditions. The scale of this undertaking was substantial, requiring the installation of 160 tons of prefabricated steel, meticulously distributed with 40 tons allocated to each column.
Our scope extended beyond mere installation. It encompassed a comprehensive approach, from the initial fabrication and assembly of components at our Galveston yard to the final installation and alignment of critical machinery onboard the vessel. This included precise winch gearbox and motor alignment, ensuring optimal performance and longevity, and fitting operator cabins for enhanced crew comfort and operational control.
The project commenced in early September 2024 and is expected to conclude in mid-March 2025. The fabrication phase alone, conducted at our state-of-the-art Galveston facility, demanded approximately 20,000 man-hours of skilled labor. Our team meticulously cut, prepped, and welded steel components into precise installation pieces, adhering to the highest quality and safety standards.
The logistical complexities of this project were considerable. Transporting the fabricated steel, specialized tools, and essential equipment required a carefully orchestrated multi-modal approach. 162 pallets were dispatched via 31 truck shipments from our GCES facility to the shipping company in Fort Lauderdale, Florida, with departures staggered between September 21, 2024, and January 13, 2025. From there, 13 separate sea freight shipments conveyed the cargo to Curacao, where the Independencia II was located.
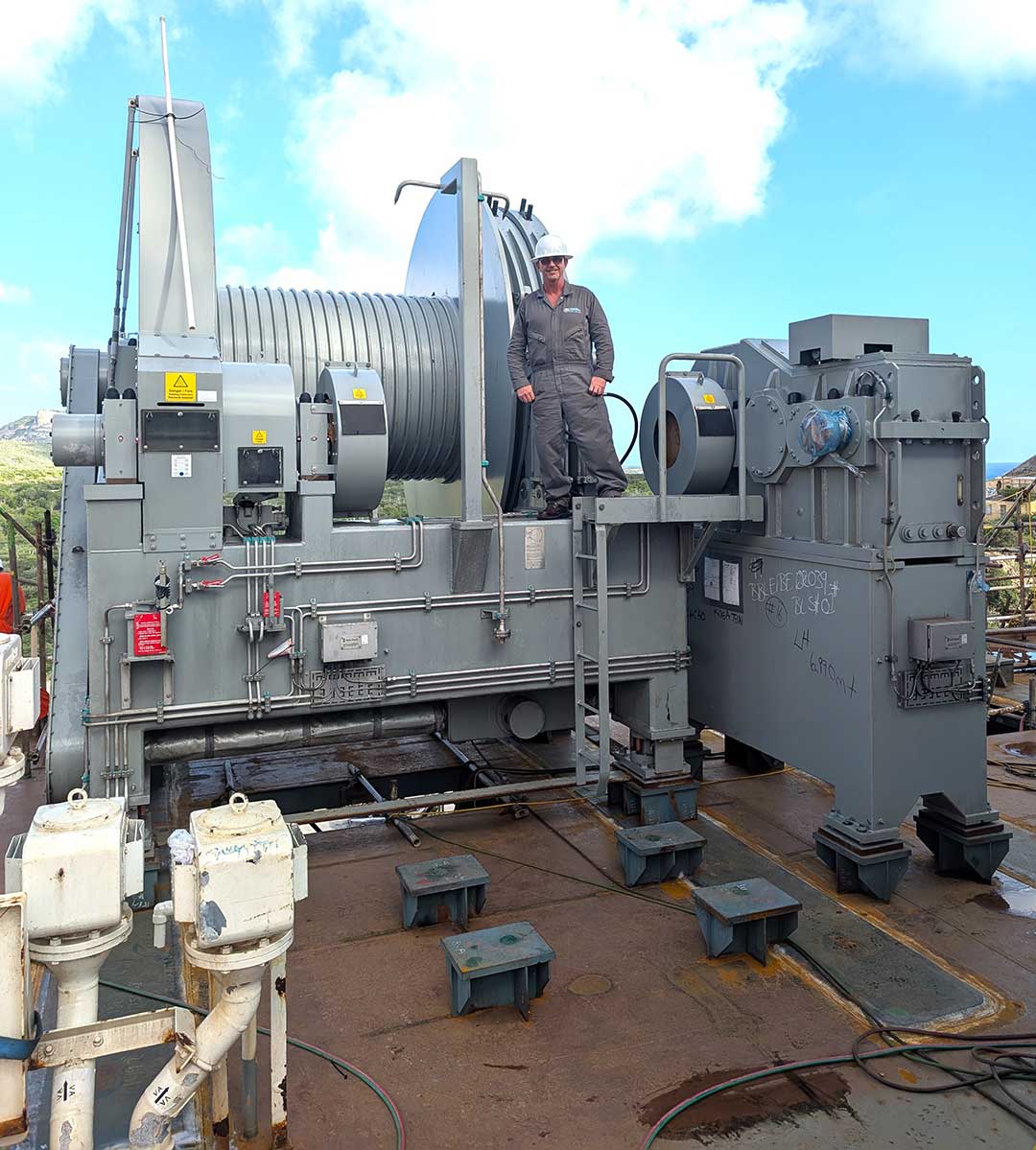
Independencia II SF Winch
On board the vessel, a dedicated team of 65 skilled professionals worked tirelessly to execute the installation. Led by Shaun Flower (Project Manager) and Emilio Guzman (Project Supervisor), the team included seven additional supervisors overseeing a highly trained workforce of welders and fitters sourced from our Mexico office. This collaborative effort resulted in approximately 70,000 onboard man-hours, encompassing the core installation and additional tasks crucial to the vessel’s operational readiness.
The success of this project is not just measured in tons of steel or man-hours but also in the positive feedback received from our client. Christopher Stephen Hawkins, Project Planner/Document Controller for OOS, commended our team’s professionalism and near-perfect safety record. He specifically highlighted the strong leadership of Shaun and Emilio, recommending them for advancement, and praised the dedication and skill of the entire welding and fitting crews. Further feedback from OOS Project Manager Eddie Sarkis acknowledged the excellent quality of work, strong supervision, and the team’s adaptability in performing tasks beyond their assigned trades. He noted their willingness to assist with winch alignment and responsiveness to changing project requirements.
The Independencia II project underscores GCES’s capabilities in delivering complex, large-scale marine solutions. We are proud of our team’s dedication, expertise, and commitment to safety and quality, and we look forward to continuing to provide innovative solutions for the maritime energy sector.
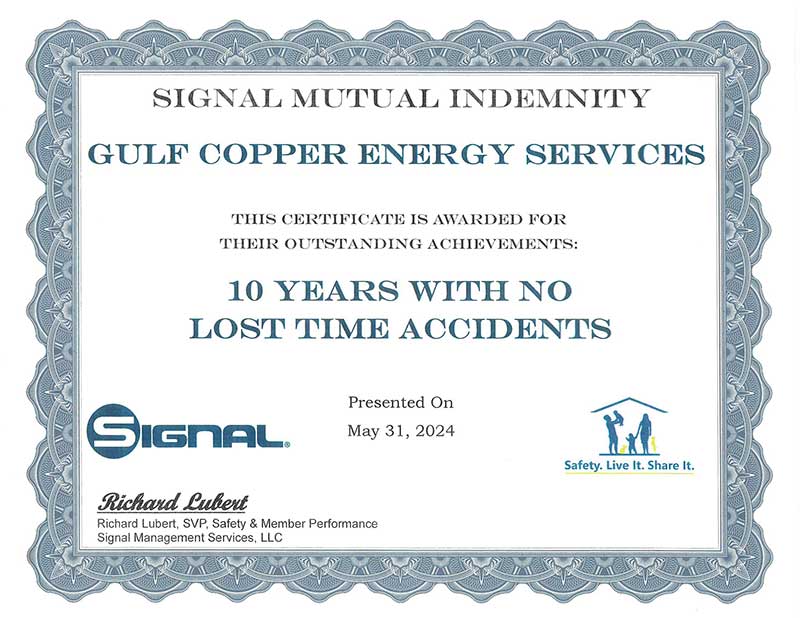
Story of the Month: GCES Celebrates a Decade of Safety Excellence
Gulf Copper Energy Services (GCES) recently received a prestigious merit certificate from Signal Management Services, marking an impressive milestone: ten years without a Lost-Time Incident (LTI). This achievement underscores GCES’s unwavering commitment to safety in the offshore and marine shipping industries’ challenging and often high-risk environments.
Senior GCES management proudly accepted the award on behalf of the dedicated employees whose daily vigilance and commitment to safe practices made this milestone possible. This accomplishment is not merely a statistic; it represents countless hours of training, meticulous planning, and a shared culture of prioritizing safety.
GCES recognizes that safety is an ongoing journey. While celebrating this remarkable accomplishment, the company reaffirms its commitment to continuous improvement. It constantly seeks opportunities to enhance its safety protocols and empower employees to work in the safest possible conditions. This dedication protects the workforce, fosters operational efficiency, and strengthens GCES’s reputation as a reliable and responsible partner in the energy sector.
Congratulations to Gulf Copper Energy Services on this outstanding achievement!
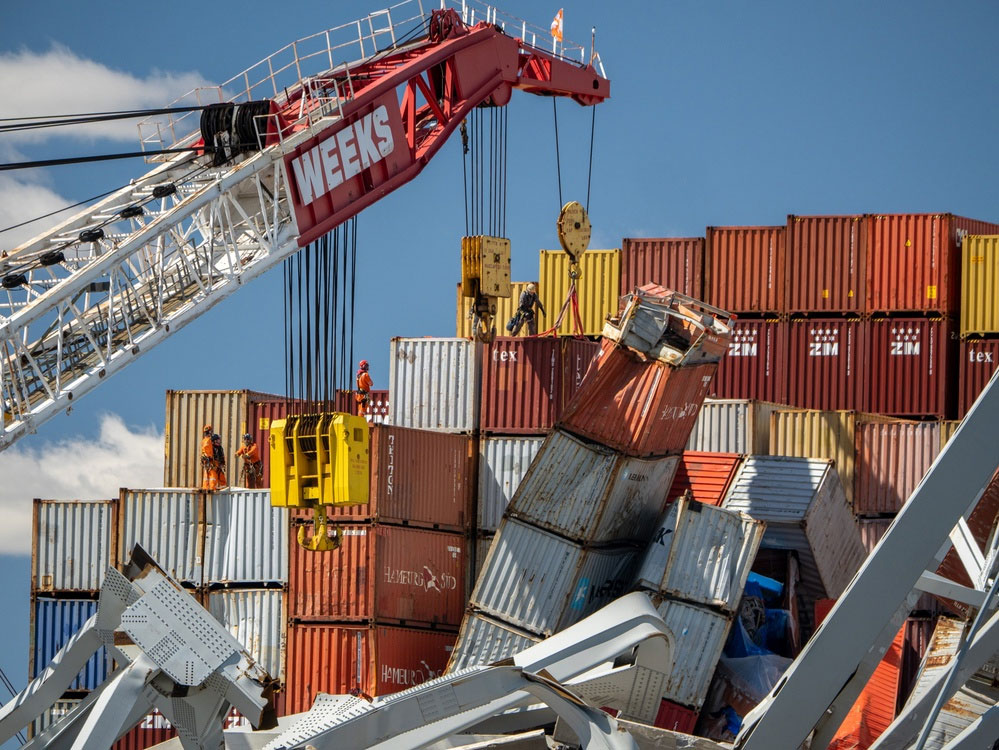
Story of the Month: GCES Rope Teams Rise to the Challenge
Gulf Copper Energy Services Rope Teams Rise to the Challenge at Dali/Baltimore Bridge Incident
When disaster strikes, Gulf Copper Energy Services (GCES) is ready to respond. This month, our highly skilled rope access team demonstrated their expertise and dedication in a critical situation involving the Dali/Baltimore Bridge. When a vessel collided with the bridge, causing significant damage and threatening the integrity of the structure, GCES was called upon to provide essential rigging support for the removal of unstable cargo containers.
Our rope team, renowned for their experience in challenging environments, worked tirelessly alongside other emergency responders to secure the area and develop a safe removal plan. Using specialized rigging techniques and their in-depth knowledge of rope access systems, our team safely removed the containers, preventing further damage to the bridge and ensuring the safety of everyone involved. This swift and effective response is a testament to the professionalism and dedication of our GCES rope access team, highlighting Gulf Copper’s commitment to providing exceptional services in even the most demanding situations.
Offshore Wind Feeder Barge conversion
Gulf Copper delivers a successful project for Van Oord, with the Offshore Wind ‘Feeder Barge’ conversion from our Port Arthur shipyard.
Thank you Van Oord, for your trust.
Many thanks to Rick Bruinsma for your support and assistance throughout the project.